Challenges to manufacturing sector in digital transformation
Much work has gone into boosting digital transformation in Vietnam’s manufacturing sector, but for many companies the process has proved problematic.
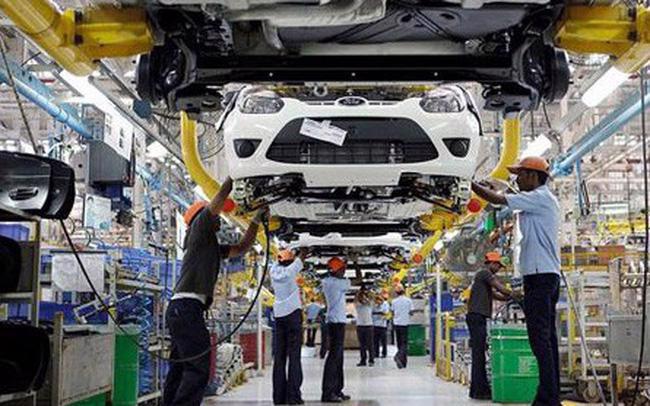
The implementation of digital transformation throughout Vietnam’s supporting industries and manufacturing sector continues to face significant challenges. The readiness to adopt Industry 4.0 technologies in production activities remains low, with many businesses struggling with issues such as a lack of digital skills, inadequate information technology (IT) infrastructure, and an absence of a digital mindset. At a recent seminar entitled “Digital Transformation towards Smart Manufacturing: Opportunities for Vietnamese Enterprises”, experts highlighted that digital transformation in the manufacturing sector is crucial. While it presents many opportunities, however, the challenges are also considerable.
Opportunities to jump ahead
Mr. Chu Viet Cuong, Director of the Industrial Development Support Center (IDC) at the Ministry of Industry and Trade (MoIT), emphasized that the opportunity lies in businesses being able to “leapfrog” others and also receive government support for their digital transformation efforts. Each year, MoIT launches programs and plans on supporting industry development, through which businesses receive expert support and guidance to enhance their production capabilities. Training programs are also conducted regularly, covering not only management and technical skills but also giving businesses the tools to adopt new technologies and business models.
Another advantage is Vietnam’s abundant and young workforce, which is quick to absorb new knowledge and innovations. Furthermore, expanding international relations allow Vietnamese businesses to connect with global companies and major corporations like Samsung, Toyota, and Honda, offering opportunities to learn from their experience.
Several successful digital transformation models are already in place. One example is the Hanel Production and Import-Export Joint Stock Company. Mr. Tran Duc Tung, Deputy General Director of Hanel PT, said the company began embracing digital transformation and smart data management back in 2010. At that time, it made a significant investment in enterprise data management systems and transitioned from a traditional, assembly-based production model, which made up 80-90 per cent of operations, to a more centralized, automated, and smarter production process. Hanel PT successfully increased its automation rate to 60 per cent, with manual assembly now accounting for only 40 per cent. Today, it has achieved 300 per cent growth in revenue, and international clients, particularly from Japan, continue to trust the company and place additional orders.
However, digital transformation in manufacturing businesses remains difficult due to limited internal capacity. Most industrial and supporting industry companies in Vietnam are small and medium-sized enterprises (SMEs), and their financial resources are insufficient. Investing in new manufacturing technologies requires substantial funds and high-quality human resources to learn and implement advanced technologies. Moreover, businesses face challenges in adopting international standards and quality management processes. “Digital transformation is not easy; the biggest challenge for any business is the commitment of leadership,” Mr. Tung said. “If the leadership does not have a clear strategy or lacks determination, the transformation will not succeed.”
Furthermore, during the digital transformation process, businesses require personnel who understand digital transformation deeply. Only employees within the company can truly grasp the health and condition of their business and know how best to apply digital tools. Additionally, digital transformation is expensive and requires significant investment, with limited short-term returns. These are new areas that demand both technical expertise and skilled personnel.
Mr. Nguyen Van Minh, Project Manager at the AMA Holdings Investment Joint Stock Company, is of a similar mind. He noted that when digital transformation was first introduced, its leadership team already had plans and intentions in place. Therefore, the question of what digital transformation entails and how to approach it was partially defined. However, determining how to start, where to begin, and what steps to take remained a challenge.
Businesses are often unsure of where to start. Most are still using traditional methods, with production processes documented, typed, printed, and passed between departments. However, with digital transformation, while management can quickly adapt, workers and production line managers require more time for training and supervision.
Seeking support
To stay abreast of digital transformation trends, there is widespread consensus that companies must invest in advanced technologies and infrastructure, such as big data and the Internet of Things (IoT). In addition, businesses need to focus on training their management teams and staff in relevant skills and technologies, while also developing leadership with a strategic vision. Enhancing international partnerships with major corporations is also key, as it enables businesses to accelerate their adoption of digital transformation in production and move toward sustainable development and energy efficiency.
Mr. Tung argues that to speed up the process of digital transformation and smart manufacturing, companies need substantial support from both the government and other stakeholders. Though the MoIT and the government are already offering financial and training programs, businesses have called for more streamlined and specific measures.
In terms of financial support, companies hope to gain access to favorable financial packages with better loan terms and simplified application procedures. Additionally, funding for research and development (R&D) is needed. The government could establish policies to support a group of businesses, allowing them to better compete with FDI companies.
Mr. Tran Kien Dung, International Labor Organization (ILO) expert and Director of ProfM Vietnam, explained that while many companies have successfully adopted digital transformation, there have also been many failures. He emphasized that 80 per cent of businesses fail due to hasty decisions made without a clear strategy or roadmap. Besides strategy, issues like internal capabilities, technology, human resources, and finances are major constraints.
Many still view digital transformation as a complete overhaul of the business model, with full digitization, new production methods, and enhanced customer experiences. However, this requires significant investment over the long term. Digital transformation is a gradual process. It starts with digitizing data, then production and management processes, before shifting to changes in the business model.
According to Mr. Dung, the main challenge for Vietnamese businesses is that they still perceive digital transformation as a far-off idea. They imagine it as fully automating factories with minimal staff, which is an unrealistic expectation.
For Vietnamese businesses to successfully transition to digitalization and smart manufacturing, Mr. Dung emphasized that they must implement changes in two key areas: IT and OT (Operational Technology). These two technologies must operate simultaneously and be fully integrated.
Specifically, businesses need to standardize their production environment and management systems. Processes must be restructured, optimized, and run smoothly to collect accurate, clean data. The production environment also needs to be reorganized, followed by the standardization of production flows. Only then can businesses begin digitizing the data collected and integrate IT and OT seamlessly.
Acknowledging the challenges businesses face, Mr. Cuong noted that the government is working to support them by providing financial resources such as loans and tax incentives. In the months to come, the MoIT plans to continue refining the legal framework for digital transformation by reviewing, proposing, and amending relevant legal documents.
It will also roll out a program to support industrial production aimed at applying Industry 4.0 technologies, with the goal of advancing to smart factory development by 2030. “We will continue to support businesses by training technical staff on digital transformation, which will help raise awareness within companies,” he explained.
Local authorities and relevant agencies will also work to minimize administrative and legal barriers, enabling businesses to more quickly adopt digital transformation and smart factory technologies. For financial institutions such as banks, Mr. Cuong suggested offering tax incentives and long-term loans at lower interest rates. Industry associations should also play a crucial role in connecting businesses, facilitating the exchange of knowledge on digital transformation and the adoption of smart factory management models in production and management.