Vietnam remains attractive to Nordic companies
Vietnam is keen to maintain its reputation among Nordic companies as a manufacturing powerhouse.
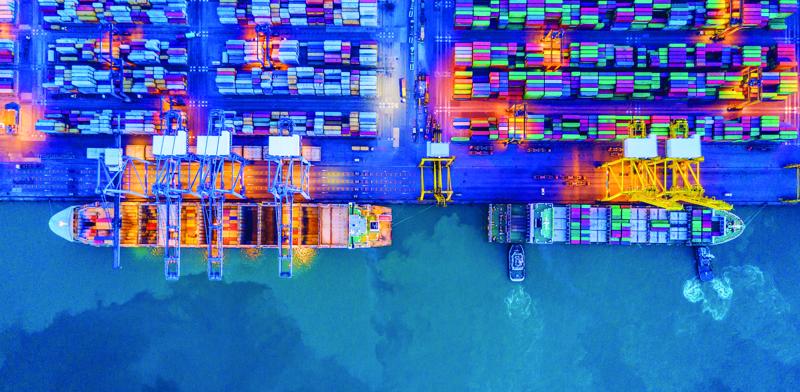
Vietnam has remained a vital manufacturing hub for Nordic businesses for decades, attracting investors in sectors from high-end jewelry to shipbuilding. With a strong industrial base and growing expertise, it continues to adapt to shifting global supply chains and evolving regulatory landscapes.
According to H.E. Johan Ndisi, Ambassador of Sweden to Vietnam, Nordic countries share a meaningful partnership with Vietnam, guided by a forward-thinking approach. Their embassies work closely together, and they see tremendous potential in Vietnam’s pivotal 2025. “If I were to describe Vietnam in one word, it would be transformation, and that is precisely what we can expect beyond the coming year,” Ambassador Ndisi highlighted, noting that Vietnam’s growth in manufacturing, paired with its energy transition, has already demonstrated the country’s ability to embrace change and establish itself as a reliable hub for international businesses, including those from Scandinavia.
Yet, as the global economy shifts, so too must Vietnam’s manufacturing sector. The country stands at a crossroads, navigating economic uncertainties while unlocking new opportunities in sustainability and digital transformation. Known for their expertise in green technologies and responsible business models, Nordic companies are eager to collaborate with Vietnam on this journey.
Key factors driving growth
Vietnam’s rise as a leading manufacturing hub in Asia has been nothing short of remarkable. Several factors have contributed to this success, making the country an attractive destination for global businesses, including Nordic companies. “From a manufacturing perspective, the three key success factors have been a competitive workforce, a skilled workforce, and affordable wages,” said Ms. Anastacia Howe, Sustainability & Public Affairs Manager at H&M in Vietnam and Cambodia. “This makes the country highly attractive for companies seeking to establish or relocate production facilities, particularly in labor-intensive industries.”
Equally important has been Vietnam’s production capabilities, which align closely with global standards, Ms. Howe believes. The development of Vietnam’s infrastructure has allowed for the expansion of its industrial capacity, positioning the country as a critical hub for manufacturing in Asia.
In addition to its workforce and production strengths, she went on, Vietnam has benefited from free trade agreements (FTAs), particularly the EU-Vietnam Free Trade Agreement (EUVFTA). The deal has significantly improved market access for European businesses, providing favorable conditions for companies like H&M to expand their operations in Vietnam.
Meanwhile, Mr. Sivert Skårn, General Director at shipbuilders Vard Vung Tau, pointed out that Vietnam’s willingness to learn and adapt has been one of the most important factors in its success. “Combining a relatively low-wage workforce with this makes it an attractive destination, especially for labor-intensive industries,” he said.
He also emphasized Vietnam’s political stability, which has played a crucial role in attracting foreign investment. Since the country joined the WTO in 2007 it has continued to strengthen its position in the global market. Its political environment, which is generally free from major disputes with other countries, has made it a reliable and secure location for businesses to invest and operate in.
Another key factor in Vietnam’s success is its strategic location. Mr. Søren Pedersen, CEO of Julie Sandlau Vietnam and Vice Chairman of NordCham Vietnam, pointed out that the country’s geographic location in Southeast Asia plays a significant role in its appeal to foreign investors. “Vietnam is strategically placed in the middle of Asia, and its location is key for logistics,” he explained. This central position allows for easier access to key markets across the region, making it an ideal logistics hub for businesses that need to move goods quickly and efficiently.
Navigating rising labor costs
Vietnam’s rapid rise as a manufacturing powerhouse has long been driven by its competitive labor costs. However, as it continues to grow in prominence, rising wages are becoming a challenge for many manufacturers, and they must find ways to remain competitive while maintaining high-quality production. “Vietnam was once the cheaper destination compared to India and Thailand, but now wages are increasing at a higher rate than in neighboring countries,” Mr. Pedersen said. For manufacturers, managing a consistent 5 per cent annual increase in labor costs is not sustainable through cost-cutting alone.
In response to rising labor costs, his company has focused on incorporating technology and automation to maintain productivity and reduce its reliance on manual labor. However, some sectors, like jewelry-making, are particularly labor-intensive, requiring skilled artisans to produce high-end pieces. This combination of rising wages and a lack of specialized training infrastructure creates a unique challenge, but companies like Julie Sandlau are mitigating such risks by setting up internal education programs and prioritizing long-term employee retention.
Mr. Skårn highlighted a similar issue. While some positions, such as welders and electricians, are relatively easy to fill through in-house training, the shortage of highly-skilled workers, particularly in niche industries like shipbuilding, remains a significant challenge. “In the south of Vietnam, only 25 or so new graduates per year are trained in naval architecture and marine engineering,” he explained. This lack of qualified engineers poses a barrier to expanding specialized industries, like shipbuilding, that are crucial to Vietnam’s broader economic development.
Some companies have found ways to adapt to the changing employment landscape by embracing partnerships with strategic suppliers. For example, H&M is focusing on compliance and social responsibility in managing labor costs. The company has strict requirements around workplace standards and wages for suppliers, ensuring fair wages and consistent annual increases. Its approach emphasizes the importance of a partnership model, where companies and their suppliers work together to navigate rising labor costs without compromising on labor standards or product quality. This partnership model can help secure sustainable growth, even as wage pressures mount.
Adapting to global supply chain challenges
As the world’s supply chain landscape evolves, businesses worldwide are grappling with disruptions triggered by the pandemic, geopolitical tensions, and the introduction of new regulations. In this context, Nordic companies are embracing strategies to remain resilient while navigating these challenges. From supplier relationships to innovation and sustainability, they are adapting with agility to ensure their operations continue smoothly.
At H&M, the importance of supply chain transparency is increasingly underscored. “For years, we focused on Tier 1 and Tier 2 suppliers,” Ms. Howe explained. “But today, to comply with new regulations like the [EU’s] Corporate Sustainability Due Diligence Regulation (CSDR), we are expanding our scope to cover the entire supply chain.”
With new regulations requiring greater accountability and sustainability, brands must ensure they are fully aware of practices at every level of their supply chain. Ms. Howe noted that a collaborative approach is key. Working closely with suppliers and aligning on common standards can help reduce the burden of compliance and increase the efficiency of the process. This shared responsibility allows brands to navigate the complexities of supply chain due diligence without overwhelming individual suppliers, especially in regions where supply chains are heavily interconnected.
Meanwhile, Mr. Skårn explained how global disruptions are prompting businesses to rethink their reliance on distant supply chains. “The pandemic and geopolitical tensions have shown us the risks of relying on global supply chains,” he shared. “That’s why we’re now focusing on regional and local sourcing, reducing the dependency on distant markets.” By shifting towards local and regional suppliers, companies can minimize delays and manage risks more effectively. However, it also means navigating new challenges, including adapting lead times and adjusting warehouse capacities to meet new sourcing models.
Reflecting on the challenges for European businesses, Mr. Pedersen addressed rising concerns over investment in emerging markets like Vietnam. “There is hesitation among European companies to make investments until they can be assured that their green ambitions align with local capabilities,” he said. Despite the Vietnamese workforce’s readiness to embrace sustainability, he pointed out that a lack of infrastructure and alignment with green policies could affect potential investments.